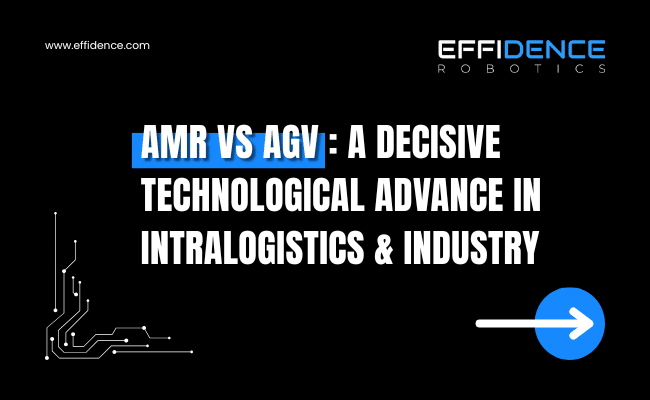
AMR vs AGV : a decisive technological advance in intralogistics & industry
Definitions
AGVs
The globalization of industry introduced the use of the first robots, AGVs (Autonomous Guided Vehicles), robots that follow a predefined path and are guided by physical elements (wires on the ground, beacons) or virtual elements.
AMRs
In recent years, a new generation of robots has become widespread: AMRs (Autonomous Mobile Robots) or AIVs (Autonomous Intelligent Vehicles). These robots are directly equipped with an intelligent navigation system, enabling them to navigate their environment completely autonomously, without any guidance system.
Once they have a map of the site, including the landmarks they need to find their way around, the robots choose which paths to take based on a number of criteria (distance, congestion, etc.).
AMR technology
SLAM (Simultaneous Localisation and Mapping) technology enables the navigation system to locate itself in real time as the robot moves forward. This is achieved by constantly comparing the vision data recorded by the sensors with the pre-installed map.
AMR vs AGV : towards a smarter and more flexible automation
Ease of integration and operational flexibility
- Autonomous navigation thanks to SLAM (Simultaneous Localization and Mapping): no need for fixed infrastructure.
AMRs are simpler and more cost-effective to install than AGVs, eliminating the work required to install guidance systems.
As the installation is based almost exclusively on software mapping, it will leave no footprint on the infrastructure, making it easier to make changes.
- Rapid adaptation to changing environments (layout modifications, adding stations).
Modifying a scenario, a trajectory or even the layout of a site is just a few clicks away.
AMRs can therefore evolve in a changing environment and adapt perfectly. What’s more, unlike AGVs, when an AMR comes up against an obstacle, it can go around it and choose another route to reach its destination. It won’t get stuck.
- Multi-site deployment made easy.
Adaptability and safety
Thanks to their multiple sensors, AMRs can instantly adapt to their environment, to avoid an obstacle for example.
The fleet coordinator will also be able to further optimise the robots’ journeys by intelligently managing them.
AMRs /AIVs are also simpler and more economical to install than AGVs, eliminating the work required to install guidance systems.
Lower costs
- Less maintenance than AGVs (no rails or beacons to maintain).
- Less reliance on infrastructure (reduced installation costs).
AMR benefits
This new era of assistants is a real time-saver. They increase productivity and streamline operations while working alongside your operators. These robots take care of repetitive tasks so that your operators can concentrate on their value-added tasks, while protecting their health and reducing the risk of musculoskeletal disorders.
Scalability & interoperability
- Easy to scale: add new robots in just a few clicks.
- Can communicate with WMS / MES / ERP and internal systems (automatic doors, call buttons, etc).
- Integration into 4.0 industrial ecosystems.
Visibility & traceability
- Real-time tracking of missions, positions, load status (with the fleet manager, such as our EffiFCS).
- History of journeys and usable KPIs (mission time, availability rate).